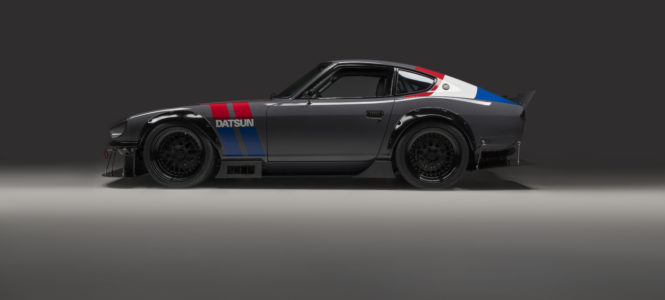
“InZanity” ’72 Datsun 240z
- The digitized version of what I have been seeing since the get go
- The goal was to modernize the 240z without losing its soul. I think mission accomplished
- look at the style lines, those are crisp and accurate
- fresh out of the booth, ready for color sanding and buff
- laying out ideas for some vinyl graphics. much tape was wasted, but I created a design that works from all angles and looks great
- modern electronic power steering with adjustable input… in a 72 240z
- the highlt modified rear differential cover.
- one of my favorite pieces, this light gauge alloy shield hides the rear differential cooler behind the wheel
- no room to spare
- details you will see from outside the car
- I designed these custom cnc snout oilers to hugely upgrade the differential oiling system
- fresh powdercoated goodies ready for assembly
- One hell of a well executed design if you ask me
- my favorite color ever, it brings this chassis decades ahead, dare I say to modern times
- these colors should play very well together. A bit more interesting than plain satin black
- a taste of what is to come…
- I rolled the LS1 plant out into the sun for inspection
- A quick wet up shows how tight the style lines are after just 400 grit
- All those hours surely were worthwhile
- You see this in your rear view, its already too late
- I met the flared hole quota on this cage I do believe
- An interior that means business
- Finish welding the strut tower center support
- A rear fuel cell firewall with a twist
- Presto, electric power steering on a Woodward column. All hidden under the dash.
- layers upon layers of custom fabrication and planning
- Unreal to see the exterior of the Z at this stage
- High performance can also be beautiful
- 2.5″ Pie-cut stainless exhaust, back purged and tig welded to perfection
- yes, thats an exhaust pipe
- Applying a bedliner coating to the belly of the beast
- so many one-off hand made pieces. It brings me great joy to do this styff by hand
- precision sectioning the woodward steering column to accept the EPAS Power steering motor
- I machined a weld on shim to accept the O.D. of the EPAS shaft and the I.D. of the Woodward column
- Tig welding the shim to the motor
- seam sealing the bottom side seams
- LS1 looking fresh with the Holley coil on cover Valve covers and LS3 Coils
- Re-assembling the engine after paint
- Getting the interior and engine bay sprayed with a light gloss grey paint
- The cage work looks tidy with a uniform color
- Satin bronze for the LS1 Block and heads
- EPAS electric power steering should make driving this beast a bit more tamable
- The front rear diffuser bracket, 100% hand made by me, no cnc just a steady hand and a good tape measure
- cleaning up the custom engine mounts for a better appearance and reduced weight
- a sweet throttle body plug I made to ease with reassembly, plus it just looks good.
- Saving some weight on thes engine mounts
- Chassis jacking points built in to the bottom side of the main cage hoop tie ins, extremely strong!
- Bryan the painter after a job well done!
- A tunnel so slick I think we will leave it uncovered
- a custom tig welded rear sub mount battery box
- The factory steam port into the throttle body before removal
- A nicely detailed and cleaned throttle body, what’s missing?
- the dirty motor before cleanup
- a few hours of hard scrubbing goes a long way
- I must combine these two
- Ah, much better. All the casting marks are cleaned up too for a truely custom part
- The last round of primer
- Pretty alloy dimes on the coolant overflow tank
- Most of the custom handmade alloy parts awaiting final checks and the powdercoater
- I modified this SPA Techique fire suppression lever with a collet and pin so no accedental pulling can take place outside of a racing environment
- cool new parts to add to the list
- First round of primer blocking in the books
- final welding on the custom air intake support
- Finally, no more orange
- Quality gaps make the bodywork. I spent many hours welding and filing to perfection. All metal edges to boot.
- The peep hole I cut to access the center deck spoiler mounts
- Adding stiffness to the deck lid spoiler mounting points. Nothing ever just bolts on
- Major reinforcement and armour to the unibody main rails
- stitch welded seams everywhere topside and underneath
- aditional seam welding for torsional strength
- is that hole factory? no, no it is not
- I love good cage work
- Cleaning up the hood heat extractor vent openings
- a solid mount for the hydraulic slide lever
- The last hoorah before sealer
- Rear brake duct rocker clearancing and solid tow/jacking points
- nothing like cutting .750″ hardened steel by hand, but its for a good cause, protecting that beautiful exhaust
- reinforcing the rail exhaust cutouts
- fire suppression brackets added to the engine bay
- battery kill switch with a little flair
- The humped alloy pieces leave room and easy access to the fuel pump and check valve
- sometimes its best to walk away when a design isnt working. The abomination on the left is idea #1, need I say more?
- The steel riser gets welded to the chassis and flanged nuts welded to the backside for easy removal of the aluminum top piece. It began life as a flat sheet of 18 ga. the shrinker/stretcher did the rest
- making the tools to make the things. This was done before I purchased the electromagnetic break
- A handmade fuel filter bracket
- Hydraulic rear break lockup at the pull of a lever
- Out with the old, in with the cleaner new brake lines
- A whole lot of custom in one place
- Radiator air ducting done right. All light guage alloy and bolt on
- Inside the Brake master heat shield
- From the bottom, this will get coated with gold heat reflective material
- The prop. valve hides nicely under the master cylinder
- Im a big fan of cool brakes
- Streamlining the factory systems once again
- From inside you cant tell Datsun didnt provide this column from the factory
- tig welding the flared hole gussets to the aprons.
- I really like this functional design. those towers aren’t going anywhere
- This shows how extreme the curvature is on these cage gussets
- From concept to reality, the poormans no CAD way
- strong
- It has come a long ways, looking this clean before any finish work too
- I fabbed this custom dolly to keep the Z mobile during the bodywork stage
- The rear custom dolly stand
- MY Z06 is scared and this car doesn’t have a motor
- AZC Billet goodness
- Chemically Stripping 40ish years of paint
- It has a horn, therefore it must be a “streetcar”
- Duct work
- Keeping all that air directed where it should go for better cooling and aerodynamics
- A shield to keep tire debis off the fire tank
- This cover protects the fire bottle and directs turbulant air off the tire out the quarter panel vent, win win.
- Keeping the ultra thin guage alloy cool while welding
- The hdpe rear diffuser
- aluminum bellypan work keeps the air headed where it should
- Triming the main duct for integrated radar detection
- What’s that, don’t worry about it…
- I think she’s smiling
- Radar refractors hidden in the grill
- Dissasembly taking place
- A minor upgrade ahead of the core support
- form meets function
- DAMN, i mean dam…
- Front splitter
- the x-pipe sits in front of the oil pan sump
- pre-rear aerodynamics
- Leaving the fab shop en route to body and paint
- every angle leaves you wanting more
- beauty
- Hand cut 14 ga. brackets
- solid mounts to the body for the winglets
- Pitch adjustable rear spoiler
- rear brake duct detail
- I see you, hidden backup camera/ rearview in the dash
- Moving the filler neck from the top to the side
- air extraction alloy beauty rings
- muscular hips
- How all my bracketry starts
- Fuel tank and differential vents
- “KMC” you know the rest
- A builders perspective, each part is used to create the bigger picture
- Tidy Tig welding with my trusty ESAB machine
- Rear brake duct
- Doing things the old fashioned way, always a pleasure
- Ugly bumper bracket
- No more bumper in the rear
- shaving side markers
- making this unsymetrical recess symetrical
- The symetrical inset really sets off the rear end
- a tight fitup for the tig welding
- She has come a long way, lots left to go though
- The progression of templates
- Ground clearance leaving the driveway, no scrapes!
- Hood air vents give you a taste of whats under